The Science Behind Porosity: A Comprehensive Guide for Welders and Fabricators
Comprehending the elaborate devices behind porosity in welding is critical for welders and makers striving for impressive craftsmanship. From the structure of the base materials to the intricacies of the welding process itself, a wide variety of variables conspire to either worsen or reduce the visibility of porosity.
Comprehending Porosity in Welding
FIRST SENTENCE:
Exam of porosity in welding exposes vital insights into the honesty and quality of the weld joint. Porosity, defined by the presence of dental caries or spaces within the weld steel, is a typical problem in welding procedures. These spaces, otherwise correctly addressed, can jeopardize the architectural honesty and mechanical residential properties of the weld, bring about possible failings in the completed item.
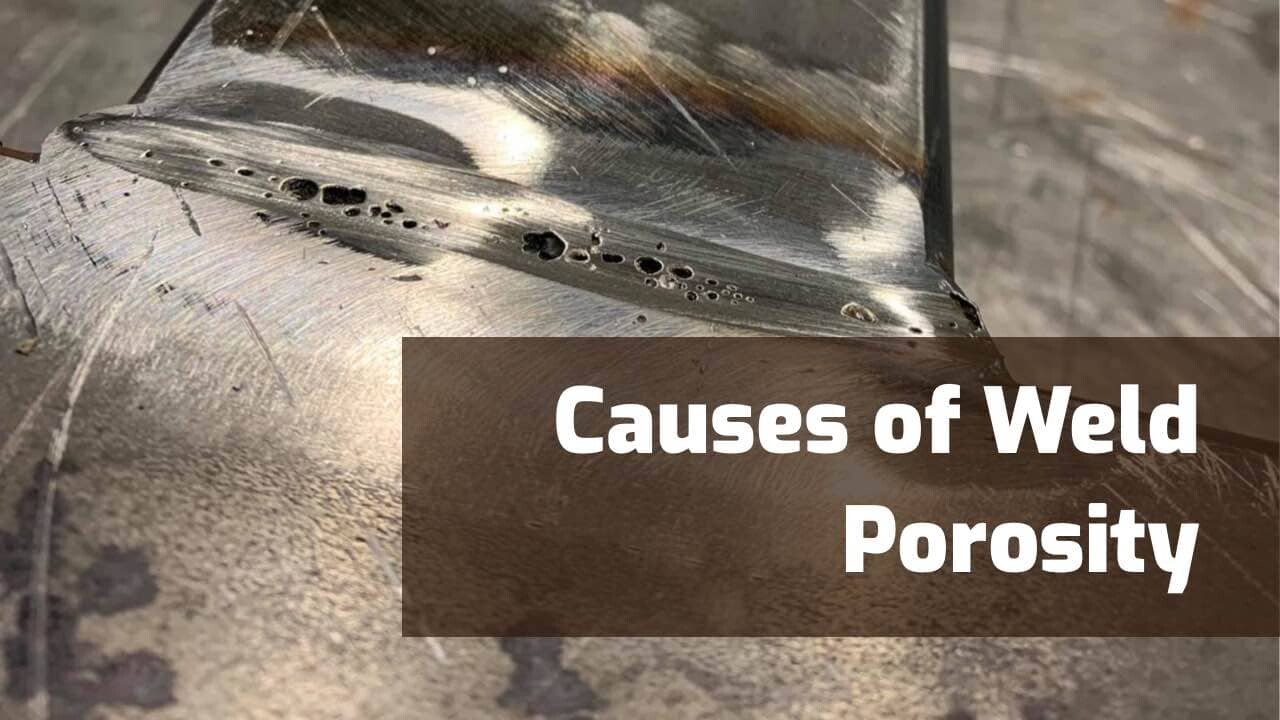
To spot and measure porosity, non-destructive testing methods such as ultrasonic testing or X-ray examination are commonly employed. These methods allow for the recognition of internal flaws without endangering the stability of the weld. By examining the size, form, and circulation of porosity within a weld, welders can make educated choices to enhance their welding processes and accomplish sounder weld joints.
Aspects Influencing Porosity Formation
The event of porosity in welding is affected by a myriad of factors, ranging from gas shielding effectiveness to the ins and outs of welding specification settings. Welding parameters, consisting of voltage, current, travel speed, and electrode type, additionally impact porosity formation. The welding strategy used, such as gas metal arc welding (GMAW) or protected metal arc welding (SMAW), can affect porosity formation due to variants in warmth distribution and gas coverage - What is Porosity.
Impacts of Porosity on Weld High Quality
The presence of porosity likewise deteriorates the weld's resistance to deterioration, as the caught air or gases within the voids can respond with the surrounding environment, leading to deterioration over time. In addition, porosity can prevent the weld's capability to hold up against stress or impact, further endangering the general high quality and integrity of the bonded framework. In crucial applications such as aerospace, vehicle, or architectural building and constructions, where security and resilience are vital, the detrimental effects of porosity on weld high quality can have serious repercussions, emphasizing the importance of minimizing porosity through proper welding methods and procedures.
Techniques to Minimize Porosity
To enhance the quality of welded joints and make certain architectural honesty, welders and producers utilize particular methods focused on reducing the development of gaps and tooth cavities within the material during the welding procedure. One reliable technique to reduce porosity is to make sure appropriate product prep work. This consists of complete cleansing of the base steel to get rid of any type of impurities such as oil, oil, or wetness that can add to porosity formation. Additionally, making use of the ideal welding parameters, such as the correct voltage, existing, and travel rate, is critical in protecting against porosity. Preserving a regular arc length and angle throughout welding likewise helps lower the possibility of porosity.

In addition, choosing the appropriate shielding gas and find this preserving proper gas flow prices are vital in minimizing porosity. Using the proper welding strategy, such as back-stepping or employing a weaving movement, can likewise aid distribute heat uniformly and lower the chances of porosity formation. Ensuring proper ventilation in the welding atmosphere to eliminate any kind of prospective sources of contamination is crucial for attaining porosity-free welds. By implementing these techniques, welders can efficiently reduce porosity and produce top notch bonded joints.
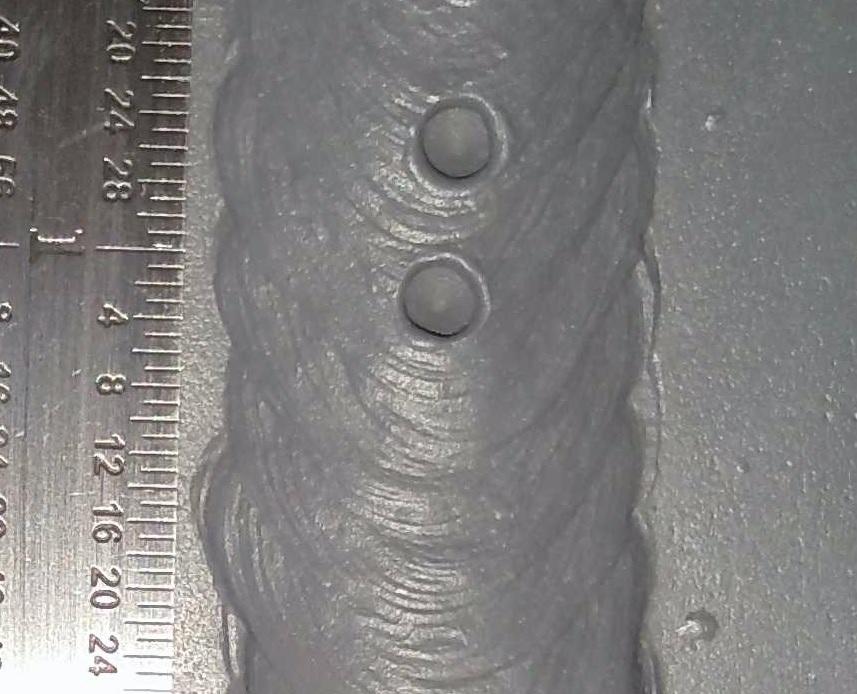
Advanced Solutions for Porosity Control
Carrying out innovative technologies and cutting-edge approaches plays a critical role in accomplishing exceptional control have a peek here over porosity in welding processes. One innovative service is the use of innovative gas blends. Protecting gases like helium or a mix of argon and hydrogen can help lower porosity by supplying better arc security and improved gas protection. Additionally, using advanced welding techniques such as pulsed MIG welding or modified atmosphere welding can additionally assist mitigate porosity problems.
An additional innovative solution includes the usage of advanced welding equipment. Making use of tools with integrated attributes like waveform control and advanced power sources can boost weld top quality and reduce porosity dangers. Moreover, the execution of automated welding systems with specific control over criteria can considerably lessen porosity flaws.
Additionally, integrating sophisticated monitoring and evaluation technologies such as real-time X-ray imaging or automated ultrasonic pop over to this site testing can assist in discovering porosity early in the welding procedure, permitting instant corrective actions. On the whole, incorporating these sophisticated services can considerably enhance porosity control and enhance the total high quality of welded parts.
Conclusion
In final thought, recognizing the science behind porosity in welding is essential for welders and fabricators to produce top quality welds - What is Porosity. Advanced remedies for porosity control can even more boost the welding procedure and make sure a solid and reputable weld.